Reducing Delays: The Importance of Reliable Material Delivery
In the world of construction and similar industries, a well-planned and reliable material delivery process carries significant weight. Efficient distribution systems act as the lifeblood of projects, ensuring that necessary materials are available when and where they are needed. They are pivotal in reducing project delays and ensuring seamless operations.
An Overview of Material Delivery Systems
Crafting a successful material delivery strategy begins with understanding the available systems. The choice of a building material delivery service can vary depending on the project's requirements, budget, and timeframe.
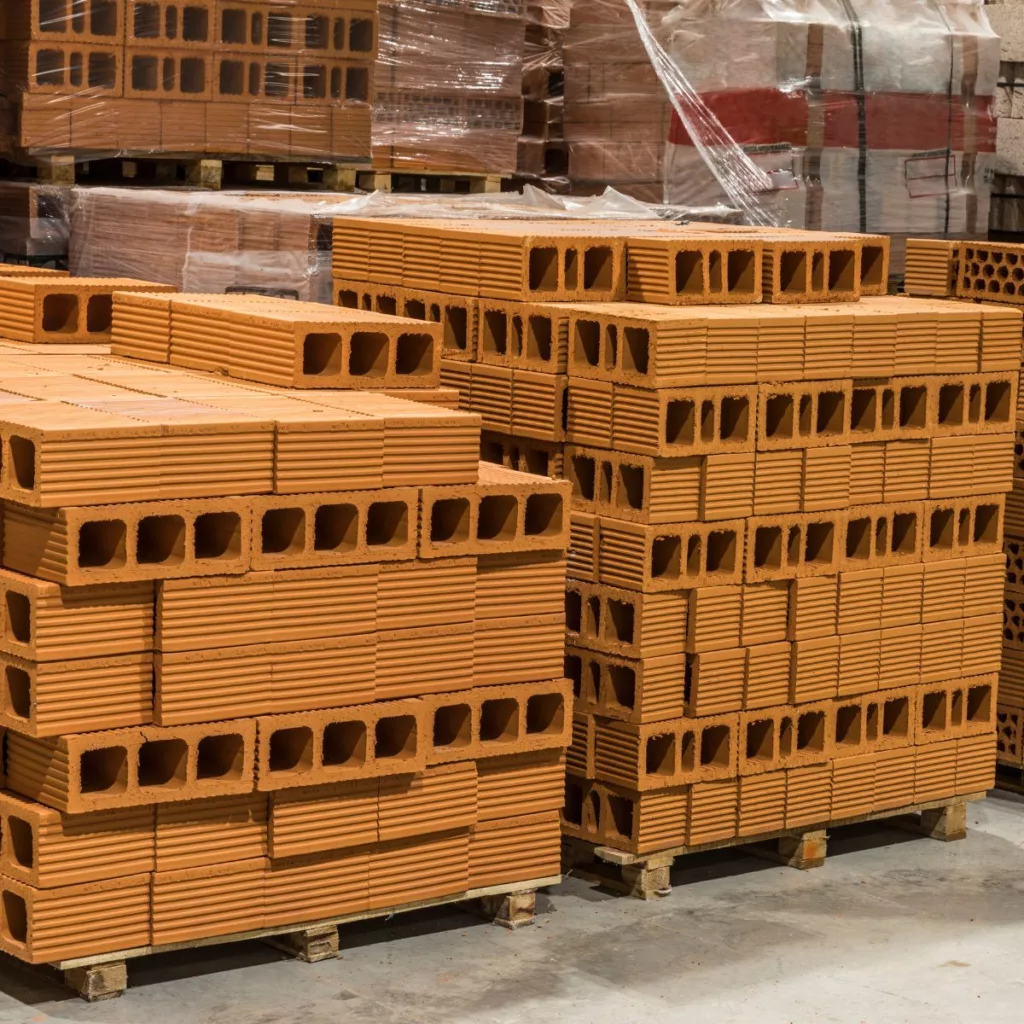
Different Types of Material Delivery Systems
Broadly speaking, there are three common types of material delivery systems used in construction: direct-to-site, centralized distribution, and on demand construction materials delivery.
- Direct-to-site Transport - This involves goods being transported directly from suppliers to the construction site. While this may seem like the most straightforward approach, it demands rigorous planning and coordination to ensure materials arrive as needed.
- Centralized Distribution - On the other hand, involves materials being delivered to a central hub or warehouse before being dispatched to various sites. This method provides a buffer for potential delays and allows for greater control over the flow of goods but incurs additional handling costs.
- On-Demand Delivery - This provides maximum flexibility, with materials ordered and delivered as needed. This system minimizes storage requirements and potential waste but relies heavily on the reliability and speed of suppliers.
The choice between these systems depends on several factors, including the nature and scale of the project, available storage space, and the reliability of the supply chain.
The Consequences of Late or Inconsistent Deliveries
Timely delivery of construction materials is an essential component of project management. Late or inconsistent deliveries can have severe implications.
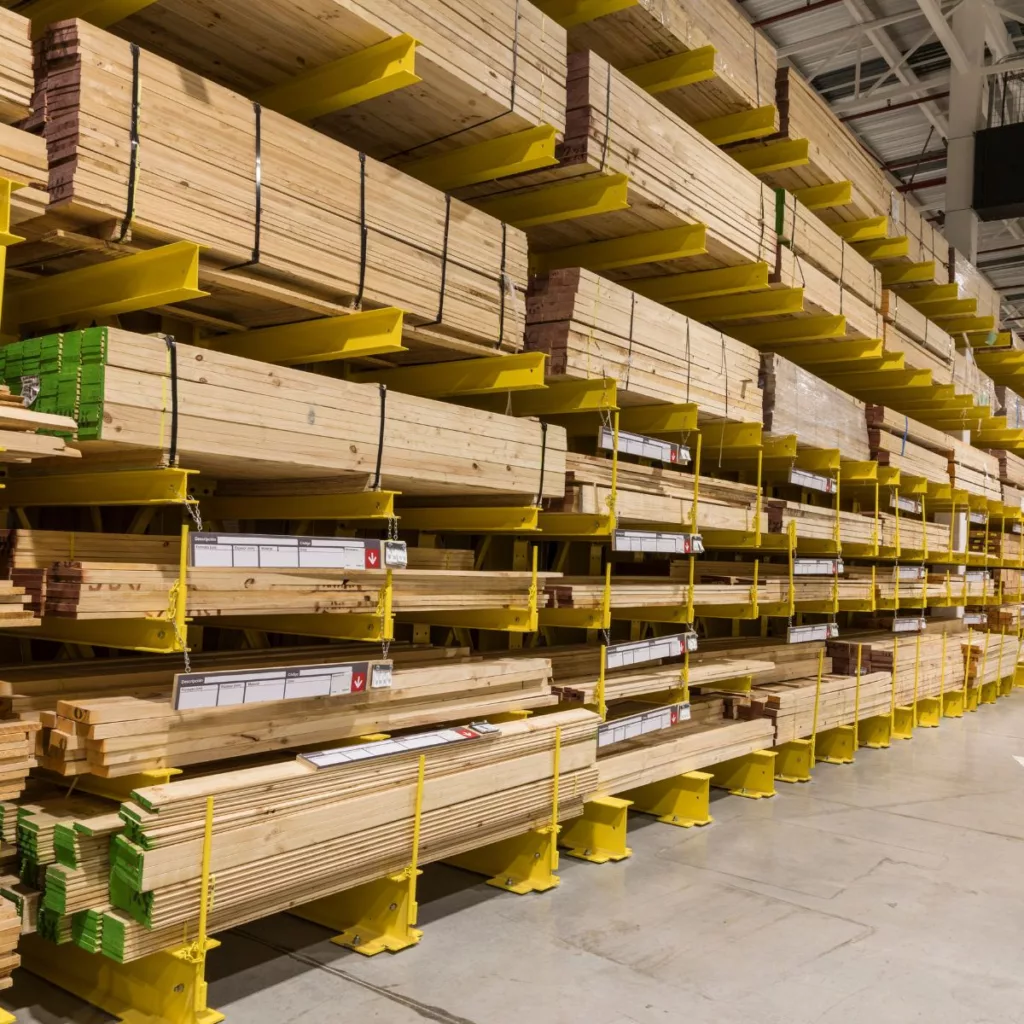
Impact on Project Timelines and Costs
Delays in construction supply delivery can derail project schedules. When the goods are late, work often comes to a halt, pushing back the project's completion date. The downstream effects can be significant – laborers may be idle, equipment rental times may extend, and penalties for not meeting deadlines may apply.
Moreover, inconsistent deliveries can also lead to cost overruns. Holding up one part of a project can cause a ripple effect, leading to increased labor and equipment costs and potentially more expensive rush orders for missing materials. Therefore, it's clear that a reliable distribution process is not just a logistical concern but a financial one too.
The Importance of Strategic Planning
Successfully navigating the building materials delivery landscape requires a keen understanding of strategic planning. Accurate forecasting and effective communication with suppliers are key.
The Role of Accurate Forecasting and Supplier Communication
Accurate forecasting plays a critical role in construction material delivery service. By accurately estimating the amount and timing of required goods, companies can ensure they have what they need without over-ordering and causing unnecessary storage and holding costs.
Alongside forecasting, communication with suppliers is equally important. Regular, clear communication can help preempt potential transport issues, allowing for proactive solutions instead of reactive scrambling.
Contingency Planning for Unexpected Disruptions
Despite the best-laid plans, disruptions can and do occur. Contingency planning helps to soften the blow of these disruptions. By planning for potential delays in material distribution, companies can minimize the impact of these delays on their projects. This might involve identifying alternative suppliers, creating buffer stocks, or adjusting project schedules to accommodate potential delays.
Building Strong Supplier Relationships
In the realm of delivery service for construction material, strong supplier relationships are invaluable. These relationships often cemented through contractual agreements, can significantly improve delivery reliability.
Importance of Contractual Agreements in Timely Deliveries
Building strong relationships with suppliers goes beyond verbal agreements. Formalizing these relationships through contractual agreements ensures that both parties are committed to meeting delivery timelines and quality standards. Contracts should clearly outline the expectations, responsibilities, and consequences in case of transport delays or inconsistencies. This not only provides a legal framework for resolving disputes but also acts as a deterrent for suppliers who may be tempted to compromise on their commitments.
Auditing and Assessing Supplier Reliability
Auditing and assessing potential suppliers before entering into contractual agreements is a crucial step in ensuring reliable delivery. There are several factors to consider when evaluating supplier reliability:
- Track Record - Research the supplier's track record by reviewing their past projects and client testimonials. Look for consistency in on-time deliveries and overall customer satisfaction.
- Financial Stability - Assess the financial stability of the supplier to ensure they have the necessary resources to fulfill their obligations. Financially unstable suppliers may face difficulties in meeting delivery schedules or maintaining consistent service.
- Capacity and Infrastructure - Evaluate the supplier's capacity and infrastructure. Do they have the necessary resources, equipment, and inventory management systems to handle your project's requirements? A well-equipped supplier is more likely to deliver goods reliably.
- Communication and Responsiveness - Pay attention to the supplier's communication and responsiveness during the evaluation process. Prompt and clear communication is indicative of a supplier's commitment to customer service and reliability.
By conducting thorough audits and assessments, you can minimize the risk of partnering with unreliable suppliers and establish a network of trusted providers.
Balancing Cost-effectiveness and Reliability
Cost-effectiveness is a critical consideration in any construction project. However, it should not overshadow the importance of punctuality and reliability in goods delivery. While it may be tempting to opt for the cheapest supplier, reliability should be a top priority. The cost savings from choosing a cheaper but unreliable supplier can quickly evaporate due to project delays, increased labor costs, and potential rework.
Striking a balance between cost-effectiveness and reliability involves evaluating suppliers based on a comprehensive set of criteria. Consider factors such as reputation, track record, distribution performance, and overall value for money. Opting for a supplier that offers a reasonable balance between cost and reliability can ensure smoother project execution and reduce the risk of delays.
The Role of Reputable Suppliers in Consistent Service
Sourcing goods from reputable suppliers is crucial for maintaining consistent and reliable service. Reputable suppliers have a track record of meeting delivery schedules, providing high-quality materials, and offering excellent customer support. They prioritize customer satisfaction and understand the importance of timely and accurate deliveries to the success of construction projects.
Working with reputable suppliers also brings the benefit of leveraging their expertise and industry knowledge. They can provide valuable insights, recommend alternative materials or delivery methods, and assist in optimizing your procurement processes.
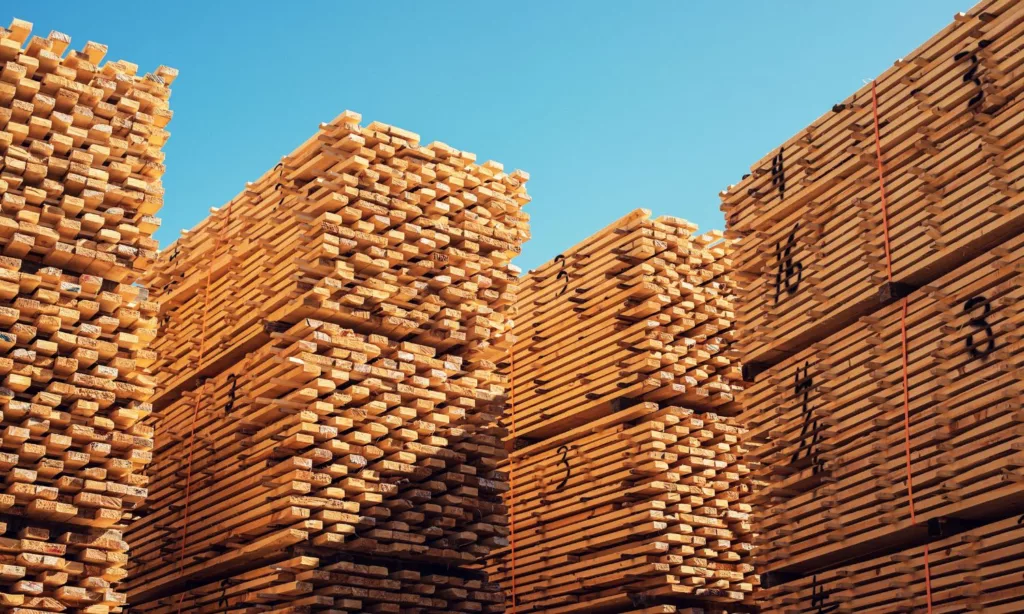
A well-planned and reliable transport process is a key factor in reducing project delays. Understanding different material delivery systems, assessing the consequences of late or inconsistent deliveries, and prioritizing strategic planning are vital steps in achieving reliable material delivery.
Building strong relationships with suppliers, backed by contractual agreements and thorough assessments, ensures consistent service. By striking a balance between cost-effectiveness and reliability, and sourcing from reputable suppliers, companies can enhance project efficiency, minimize costs, and ultimately deliver successful outcomes. Invest in creating a robust and efficient material delivery system to reap the long-term benefits of reduced delays and increased productivity.